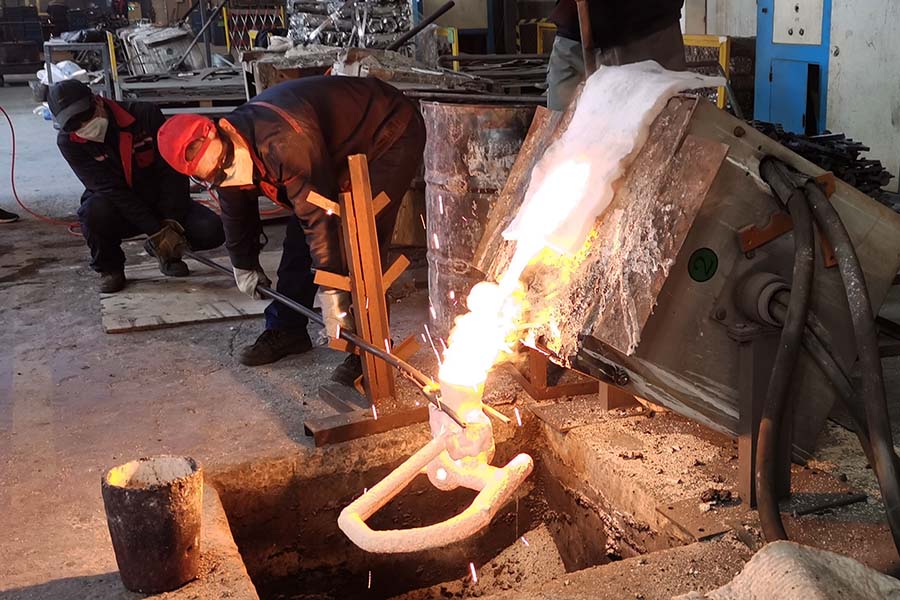
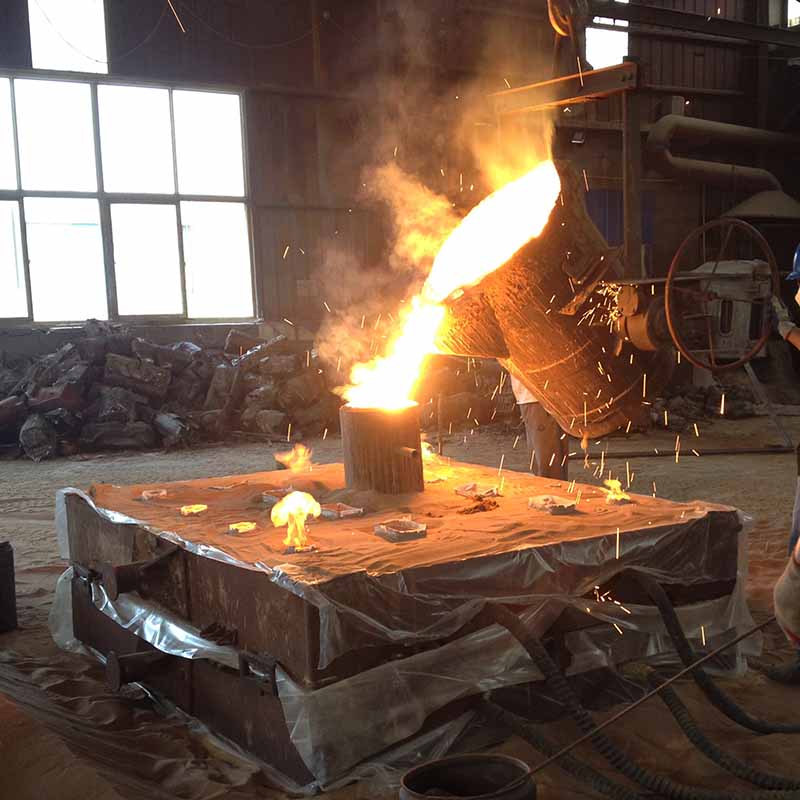
A fundición é un dos primeiros métodos de conformación de metais coñecidos polos seres humanos. Xeralmente significa verter metal fundido nun molde refractario cunha cavidade da forma que se vai facer, e deixar que se solidifique. Candosolidificado, o obxecto metálico desexado sácase do molde refractario xa sexa rompendo o molde ou desmontando o molde. O obxecto solidificado chámase fundición. Este proceso tamén se chama fundación e chámase a fábrica moderna que se centra na fundición de pezas metálicasfundición.
1. Historia do Proceso de Fundición
O proceso de fundición foi probablemente descuberto ao redor do 3500 a.C. en Mesopotamia. En moitas partes do mundo durante ese período, machados de cobre e outros obxectos planos foron transformados en moldes abertos feitos de pedra ou cocidos.arxila. Estes moldes eran esencialmente dunha soa peza. Pero en períodos posteriores, cando era necesario fabricar obxectos redondos, tales moldes dividíanse en dúas ou máis partes para facilitar a retirada dos obxectos redondos.A Idade do Bronce (c 2000 a. C.) trouxo moito máis refinamento ao proceso de fundición. Quizais por primeira vez inventouse un núcleo para facer petos ocos nos obxectos. Estes núcleos estaban feitos de barro cocido.Ademais, o proceso de cire perdue ou cera perdida foi moi utilizado para facer adornos e traballos finos.
A tecnoloxía de fundición foi moi mellorada polos chineses dende o 1500 a.C. Antes diso, non hai evidencia de ningunha actividade de fundición atopada en China. Non parecen ser xeniaisfamiliarizado co proceso cire perdue nin o usou de forma extensiva senón que se especializou en moldes de varias pezas para facer traballos moi complicados. Levaron moito tempo perfeccionando o molde ata o último detalle polo que apenasrequiríase calquera traballo de acabado na fundición feita a partir dos moldes. Probablemente fabricaron moldes de pezas que contiñan pezas coidadosamente encaixadas, con trinta ou máis. De feito, moitos destes moldes foron desenterradosrealizando escavacións arqueolóxicas en varias partes de China.
A civilización do val do Indo tamén é coñecida polo seu uso extensivo de fundición de cobre e bronce para adornos, armas, ferramentas e utensilios. Pero non houbo moita mellora na tecnoloxía. Da variOs obxectos e figuriñas que foron escavados nos xacementos do val do Indo, parecen estar familiarizados con todos os métodos de fundición coñecidos, como o molde aberto, o molde en pezas e o proceso de cire perdue.
Aínda que á India se lle podía acreditar a invención do aceiro do crisol, na India non era evidente gran parte da fundación de ferro. Hai evidencias de que a fundación do ferro comezara ao redor do 1000 a.C. en Siria e Persia. Apareceisofundición de ferroA tecnoloxía na India estivo en uso dende os tempos da invasión de Alexandre Magno, arredor do 300 a.C.
O famoso piar de ferro situado actualmente preto do minar Qutb en Delhi é un exemplo das habilidades metalúrxicas dos antigos indios. Ten 7,2 m de lonxitude e está feito de ferro maleable puro. Suponse que isto é doperíodo de Chandragupta II (375-413 d.C.) da dinastía Gupta. A taxa de oxidación deste alicerce, que está fóra ao aire libre é practicamente nula e mesmo a parte soterrada se oxida a un ritmo extremadamente lento. Istoprimeiro debeu ser fundido e despois martelado ata a forma final.
2. Vantaxes e limitacións
O proceso de fundición é amplamente utilizado na fabricación debido ás súas moitas vantaxes. O material fundido flúe a calquera pequena sección da cavidade do molde e, como tal, a calquera forma intrincada, internaou externo: pódese facer co proceso de fundición. É posible fundir practicamente calquera material, xa sexa ferroso ou non ferroso. Ademais, as ferramentas necesarias necesarias para moldes de fundición son moi sinxelas ebarato. Como resultado, para a produción de proba ou a produción dun lote pequeno, é un método ideal. É posible no proceso de fundición, colocar a cantidade de material onde sexa exactamente necesario. Como resultadopódese conseguir unha redución de peso no deseño.Castingsson xeralmente arrefriados uniformemente desde todos os sid e, polo tanto, espérase que non teñan propiedades direccionais. Hai certos metais e aliaxesque só se pode procesar por fundición e non por ningún outro proceso como a forxa polas consideracións metalúrxicas. Pódense facer fundicións de calquera tamaño e peso, incluso de ata 200 toneladas.
Non obstante, a precisión dimensional e o acabado superficial alcanzados polo normalproceso de fundición en arenanon sería adecuado para a aplicación final en moitos casos. Para ter en conta estes casos, algún casting especialdesenvolvéronse procesos como a fundición a presión, cuxos detalles se dan en capítulos posteriores. Ademais, o proceso de fundición en area é un traballo intensivo en certa medida e, polo tanto, moitas melloras están dirixidas a el,como a máquina de moldaxe e a mecanización de fundición. Con algúns materiais adoita ser difícil eliminar os defectos derivados da humidade presentefundicións en area.
3. Condicións de casting
Nos capítulos seguintes veríanse os detalles da fundición en area, que representa o proceso básico de fundición. Antes de entrar nos detalles do proceso, sería necesario definir unha serie de palabras de vocabulario de castingapropiado.
Matraz– Un matraz de moldeo é aquel que mantén intacto o molde de area. Dependendo da posición do matraz na estrutura do molde, refírese con varios nomes como arrastre, copa e meixela. Está formado por madeirapara aplicacións temporais ou máis xeralmente de metal para uso a longo prazo.
Arrastra– Matraz de moldeo inferior
Facer fronte– Matraz de moldeo superior
Fazula– Matraz de moldeo intermedio empregado na moldaxe de tres pezas.
Patrón– O patrón é unha réplica do obxecto final a realizar con algunhas modificacións. A cavidade do molde faise coa axuda do patrón.
Liña de partida– Esta é a liña divisoria entre os dous matraces de moldura que forman o molde de area. No patrón dividido tamén é a liña divisoria entre as dúas metades do patrón
Taboleiro inferior– Trátase dun taboleiro de madeira, que se utiliza no inicio da elaboración do molde. Primeiro gárdase o patrón no taboleiro inferior, espolvérase area sobre el e despois faise o apisonamento no arrastre.
Fronte á area– A pequena cantidade de material carbonoso espolvoreado na superficie interna da cavidade de moldura para dar un mellor acabado superficial ás pezas de fundición.
Area de moldeo– É o material refractario acabado de preparar que se utiliza para facer a cavidade do molde. É unha mestura de arxila de sílice e humidade en proporcións adecuadas para obter os resultados desexados e rodea opatrón ao facer o molde.
Area de apoio– É o que constitúe a maior parte do material refractario que se atopa no molde. Esta está formada por area usada e queimada.
Núcleo– Utilízase para facer cavidades ocas en fundicións.
Conca de vertedura– Unha pequena cavidade en forma de funil na parte superior do molde na que se vierte o metal fundido.
Spure– O paso polo que o metal fundido da cunca de vertedura chega á cavidade do molde. En moitos casos controla o fluxo de metal no molde.
Corredor– Os pasos no plano de separación polos que se regula o fluxo de metal fundido antes de chegar á cavidade do molde.
Porta– O punto de entrada real polo que o metal fundido entra na cavidade do molde.
Coronilla– As coronillas utilízanse para soportar núcleos dentro da cavidade do molde para coidar o seu propio peso e superar as forzas metalestáticas.
Arrefriar– Os calafríos son obxectos metálicos, que se colocan no molde para aumentar a velocidade de arrefriamento das pezas fundidas para proporcionar unha velocidade de arrefriamento uniforme ou desexada.
Riser– É un depósito de metal fundido que se proporciona na fundición para que o metal quente poida fluír de novo á cavidade do molde cando se produce unha redución de volume de metal debido á solidificación.
4. Procedemento de elaboración de moldes de area
O procedemento para facer un molde de area típico descríbese nos seguintes pasos:
En primeiro lugar, colócase unha táboa inferior sobre a plataforma de moldura ou no chan, facendo que a superficie sexa uniforme. O matraz de moldaxe de arrastre mantense boca abaixo no taboleiro inferior xunto coa parte de arrastre dopatrón no centro do matraz no taboleiro. Debe haber suficiente espazo libre entre o patrón e as paredes do matraz que debe ser da orde de 50 a 100 mm. Espolvorease area secao taboleiro e o patrón para proporcionar unha capa non pegajosa. Agora bótase no arrastre e sobre o patrón area de moldeo recén preparada de calidade requirida ata un espesor de 30 a 50 mm. O resto do frasco de arrastre étotalmente cheo coa area de respaldo e batido uniformemente para compactar a area. O apisonamento da area debe facerse correctamente para non compactala demasiado, o que dificulta a fuga dos gases,nin demasiado solto, para que o molde non tivese a suficiente forza. Despois de rematar o apisonamento, o exceso de area no matraz é completamente raspado usando unha barra plana ata o nivel dos bordos do matraz.
Agora, cun fío de ventilación, que é un fío de 1 a 2 mm de diámetro cun extremo puntiagudo, fanse orificios de ventilación no arrastre ata toda a profundidade do matraz, así como no patrón para facilitar a eliminación de gases. durante a fundiciónsolidificación. Isto completa a preparación do arrastre.
O frasco de arrastre rematado envólvese agora ao taboleiro inferior expoñendo o patrón como se mostra na foto. Usando unha mancha, os bordos de area arredor do patrón son reparados e a metade do patrón colócase sobreo patrón de arrastre, aliñándoo coa axuda de pasadores. O matraz de copa enriba do arrastre sitúase aliñando de novo coa axuda dos pasadores. A area de separación seca é espolvoreada por todo o arrastre e no patrón.
A unha pequena distancia duns 50 mm do patrón está situado un pasador de bebedoiro para facer o paso do bebedoiro. Ademais, se é necesario, gárdase o pino elevador nun lugar axeitado e unha area de moldeo recén preparada similar a aquelado arrastre xunto coa area de respaldo é salpicado. A area está completamente apisonada, o exceso de area raspada e fanse orificios de ventilación por toda a capa como no arrastre.
O perno de bebedoiro e o perno de elevación e son coidadosamente retirados do matraz. Máis tarde, a cunca de vertedura córtase preto da parte superior do sprue. O cope está separado do arrastre e calquera area solta na interface de cope e arrastredo arrastre é soprado coa axuda de fol. Agora, a capa e as metades do patrón de arrastre retíranse usando as puntas de debuxo e golpeando o patrón ao redor para ampliar lixeiramente a cavidade do molde para que oas paredes do molde non están estropeadas polo patrón de retirada. Os corredores e as portas córtanse no molde con coidado sen estropear o molde. Calquera exceso ou area solta que se atope nos corredores e na cavidade do molde é sopradolonxe usando o fol. Agora, a area de revestimento en forma de pasta aplícase por toda a cavidade do molde e os corredores, o que daría á fundición acabada un bo acabado superficial.
Prepárase un núcleo de area seca usando unha caixa de núcleos. Despois da cocción adecuada, colócase na cavidade do molde como se mostra na foto. O casco substitúese sobre o arrastre coidando o aliñamento dos dous mediante opinos. Mantéñase un peso axeitado na capa para coidar a forza metalestática ascendente durante o vertido do metal fundido. O molde agora, como se mostra na foto, está listo para verter.
Hora de publicación: 25-12-2020